Inventory control is a necessary choreography in the challenging ballet of modern business, as supply chains span the world and consumer needs change at a dizzying speed.
Inventory control is a broad discipline that oversees the movement of goods within the business. It’s the compass that directs businesses through the choppy waters of balancing supply and demand, optimizing costs, and ensuring items are ready when customers call. This article is a comprehensive guide to inventory control, delving into its definition, emphasizing its critical importance, addressing current challenges, exploring various inventory control systems and techniques, and providing actionable tips for effective inventory management.
Inventory Control – Definition
Inventory Control, also known as Stock control can be defined as the process of ensuring that a business has the right amount of stock to meet its customer demand and reduce the cost of holding inventory. and also involves coordinating and supervising the supply, storage, distribution, and recording of materials. it aims to avoid problems such as overstocking, understocking, stockouts, and inventory loss. so inventory control can be identified as the art and science of managing the delicate balance of a company’s tangible assets. It’s comparable to a symphony conductor, harmonizing the motions of raw materials, work-in-progress, and finished goods inside an organization.
Why is Inventory Control Important
Inventory control is so important in many ways. Some reasons can be represented as follows:
Cost Efficiency – Effective inventory control assists organizations in reducing the holding and carrying expenditures associated with excess inventory. Storage expenses, insurance, depreciation, and the cost of capital tied up in inventory are all part of these costs. Businesses can enhance their overall profitability by reducing these costs.
Customer Satisfaction – Keeping inventory levels at the perfect level ensures that items are easily available when customers want to purchase. Stock shortages can result in missed sales and dissatisfied consumers. Overstocking, on the other hand, can lock up capital and possibly give rise to price markdowns or obsolescence, negatively damaging the bottom line. Keeping inventory levels under control ensures customer demand is satisfied on a constant basis, increasing consumer happiness and loyalty.
Cash Flow Management – Businesses free up resources that can be reinvested in other areas of the firm, such as expansion, marketing, or research and development, by controlling inventory levels and lowering surplus. Inventory management which is effective improves cash flow, which is vital to a company’s financial health.
Minimizing Risk – Inventory control helps in the reduction of losses in inventory that result from theft, damage, or expiry. Businesses can reduce the cost impact of such losses by constantly monitoring and managing inventories.
Efficient Operations – The control of inventory ensures that production and supply chain operations function smoothly. Effective inventory control can assist in preventing bottlenecks and issues in operations, leading to improved efficiency and shorter lead times.
Strategic Decision-Making – Accurate inventory levels and turnover data provide helpful information for strategic decision-making. It helps businesses recognize trends, forecast demand, and make informed decisions about offerings of goods, suppliers, and development strategies.
6 Techniques of Inventory Control
Inventory control techniques are the strategies and methods used by businesses to effectively manage and optimize their inventory. These strategies assist in maintaining a balance between product availability and holding expenses. Here are some examples of common inventory control methods:
ABC Analysis
This method separates inventory items into three categories based on their importance.
A items are high-value, high-priority items.
The B items are of moderate importance.
C items are of low value and priority.
Businesses can then apply different control methods to each category, with a higher priority placed on A items.
Just-in-Time (JIT) Inventory
JIT is a system in which inventory is refilled only when it is required, removing holding costs and waste. It requires effective interaction with suppliers and is dependent on accurate demand forecasts.
Economic Order Quantity (EOQ)
EOQ determines the ideal order quantity that minimizes overall inventory costs by taking into account factors such as order and holding costs. It assists businesses in balancing the expenses of ordering and keeping inventory.
FIFO (First-In, First-Out)
The first in, first out (FIFO) inventory valuation approach states that the first items added to an inventory are the first ones sold or used. In other words, the cost of the oldest inventory goods in stock is matched with revenue first under FIFO. This method is often used in businesses where the items are perishable or have a limited shelf life.
LIFO (Last-In, First-Out)
This is the method of inventory valuation that implies the most recently acquired or manufactured things are the first to be sold or consumed. LIFO balances the cost of the most recently acquired inventory with revenue first. LIFO is more typical in businesses where inventory costs are steady or declining.
Cross-Docking
Cross-docking is the process of shifting received goods from inbound to outbound shipments without storing them. It is frequently used in distribution and retail to save on handling and storage costs.
Inventory control Problems and challenges
Inventory control problems and challenges might differ depending on the industry, the size of the business, and the complexity of the supply chain. However, certain common difficulties afflict all firms. Here are some of the most common inventory control issues and concerns businesses face today
1. Overstocking and Stockouts
It is an ongoing challenge to find the correct balance between having enough inventory to meet customer demand and avoiding excess stock (overstocking) or shortages (stockouts). Overstocking wastes cash and can lead to product obsolescence, while stockouts result in lost revenue and dissatisfied customers.
2. Inaccurate Demand Forecasting
Accurately forecasting customer demand is an essential part of inventory control. and the Inaccurate forecasts of demand may end up in incorrect inventory levels, increased holding costs, and stockouts. therefore, Forecasting can be challenging due to factors such as seasonality, market trends, and unforeseen events.
3. Lead Time Variability
Variability in the time it takes to restock inventory (lead time) can disrupt inventory control. Long lead times or inconsistent supplier performance could end up in stockouts, necessitating the maintenance of higher safety stock levels.
4. Supplier Reliability
Depending on outside suppliers increases the risk of interruptions to the supply chain. Supplier reliability concerns, such as late deliveries, quality issues, or capacity constraints, can lead to inventory control issues.
5. Shrinkage and Theft
Inventory control can be impacted by losses due to theft, damage, or spoilage (shrinkage). It is essential to implement security measures and monitor for losses.
To deal with these challenges, a combination of data-driven decision-making, technology, strategic planning, and coordination with suppliers and logistical partners will be needed. Businesses that handle these inventory control concerns effectively can gain a competitive advantage by lowering costs, boosting customer satisfaction, and maximizing supply chain efficiency.
Different types of Inventory Control Systems
when it comes to Inventory control systems, are instruments and processes used to efficiently manage and optimize an organization’s inventory. There are several kinds of inventory control systems, each specialized to distinct objectives and challenges.
Here are some examples of the most common types
Periodic Review System
Inventory levels are only verified at regular periods (e.g., weekly or monthly) under this method. These periodic reviews are used for organizing orders. It’s simple, but it could result in overstocking or stockouts between reviews.
Perpetual Inventory System
A perpetual system uses software and technology to keep a real-time record of inventory levels. Each transaction, whether a sale, goods receipt, or adjustment, is promptly logged in the system.
Just-in-Time (JIT) Inventory System
JIT is a method of ordering and receiving inventory just in time for manufacturing or selling. It is intended to reduce carrying costs and waste in the manufacturing process. It necessitates tight collaboration with vendors.
Two-Bin System
Each item in this system has two inventory containers. When one bin is empty, it indicates that it needs to be filled. It’s easy to implement and helps prevent stockouts.
ABC Analysis System
ABC analysis classifies inventory items according to their importance. goods with the letter A are high-priority and high-value, while goods with the letter B are moderately important and low-value. Each category receives a unique set of control measures.
Bulk Shipments and Order Scheduling
This strategy involves ordering things in mass and scheduling deliveries at scheduled times in order to reduce transportation and warehousing costs. It is frequently applied to raw materials and components.
Kanban System
The Kanban system, which originated in lean manufacturing, uses visual indicators to call for inventory replenishment. When a given amount of an item has been utilized, a signal is sent to reorder it, providing a steady supply.
The Cloud-Based Inventory Management System
A cloud-based inventory management system, often known as cloud-based inventory software, is a digital solution that manages, tracks, and optimizes inventory and related activities using cloud computing technologies. These systems are hosted in the cloud, and accessible over the internet, instead of being installed on local servers or individual computers. Here are some examples
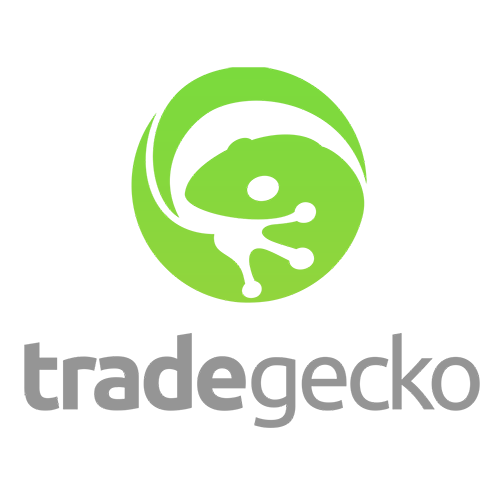
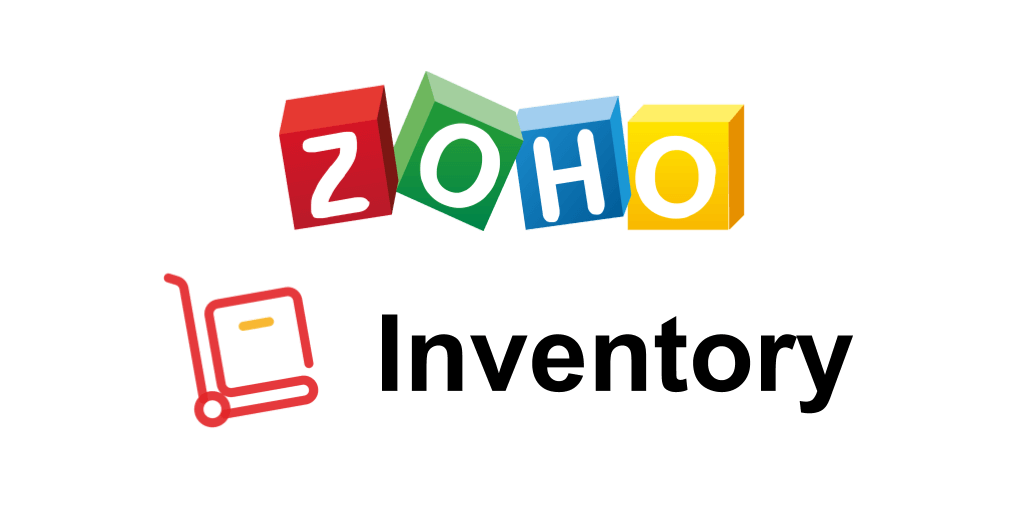
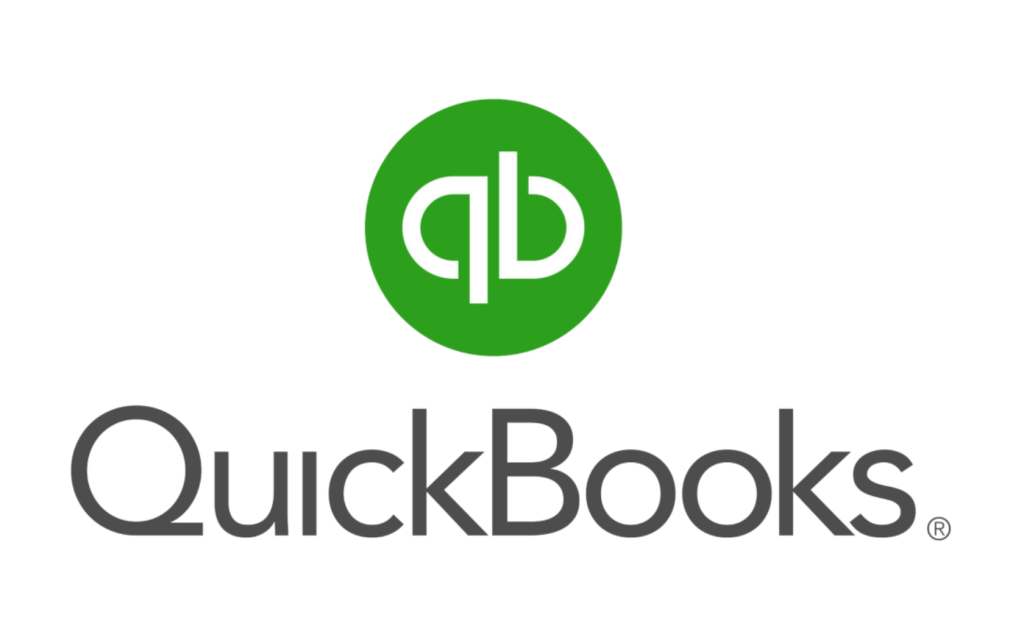
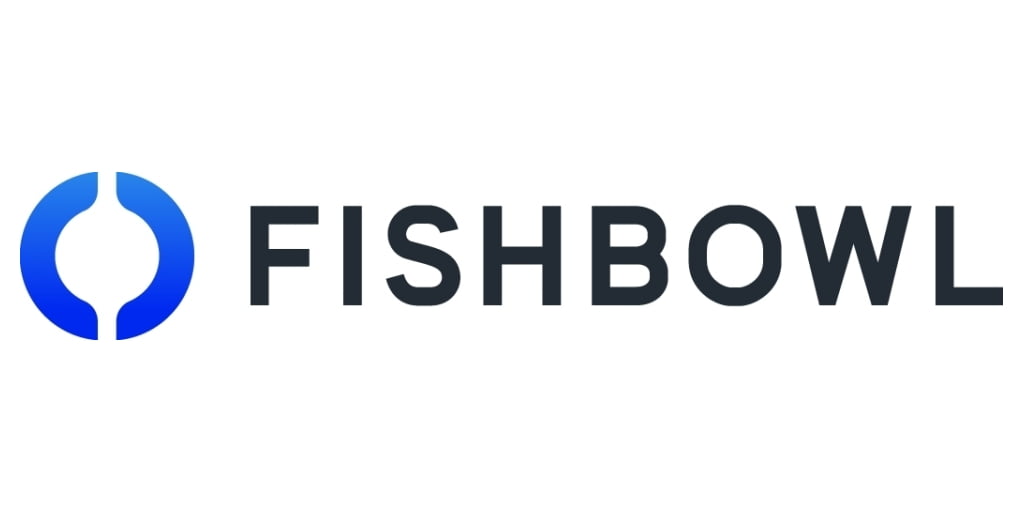
10 Tips for an Effective Inventory Control Processes
1. Make the accuracy of data a high concern. Incorrect data can lead to costly mistakes. Constantly examine and audit your inventory records to ensure their accuracy.
2. Invest in a reliable inventory management system, whether on-premises or in the cloud. Choose a solution that satisfies your company’s specific demands and capacity. Utilize your system’s features and capabilities to the utmost.
3. Use ABC analysis to classify your inventory items by importance. Focus your efforts on high-priority things (A items) to ensure their availability, while being more flexible on lower-priority items (C items).
4. Accurate demand forecasting helps you in forecasting inventory requirements and minimizes the risk of stockouts or overstocking. Refine your forecasts using historical data, market trends, and client input.
5. Set reorder points for each item in your inventory. When inventory levels reach these levels, the reordering process starts in order to maintain the right stock levels.
6. Keep a watchful eye on your suppliers’ lead times. Variability in lead times may lead to difficulties with inventory control. Create a safety stock to accommodate this unpredictability.
7. To maintain inventory accuracy, do regular physical audits and cycle counts. Implement effective auditing processes and swiftly reconcile any differences.
8. Work with trustworthy suppliers. Clear communication and agreements with suppliers can assist in improving lead times, cutting costs, and increasing supply chain reliability.
9. Maintain sufficient amounts of safety stock for items with unpredictable demand or longer lead times. Safety stock serves as a buffer against unexpected moves in demand or supply chain disruptions.
10. Align your inventory strategy with your company’s goals. Focus on inventory turnover, return on investment, and overall financial goals.